11 Reasons for Waterproofing Failure in Construction: Causes and Damages
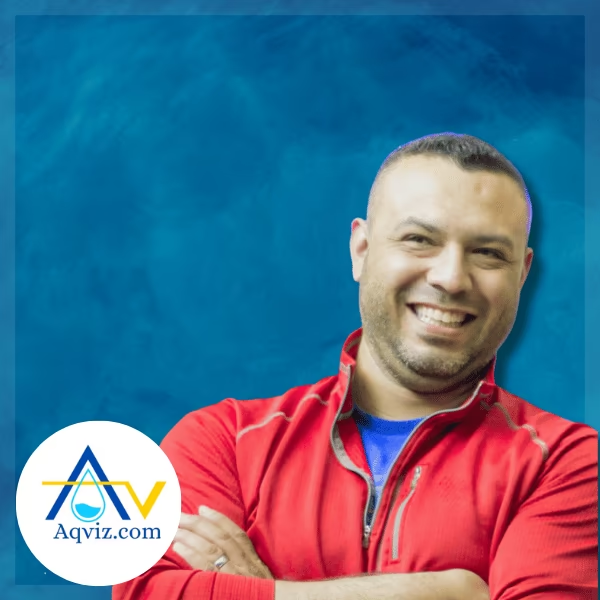
Waterproofing is laying an impervious layer on the surface in order to prevent water from leaking into the structure. When the waterproof layer is damaged due to human activities or environmental activities, accumulated water on the surface can penetrate to the building structure.
These are the most common 11 reasons for waterproofing failures in construction.
- Poor workmanship of waterproofing
- Choosing the wrong waterproof membranes
- Apply waterproof membranes on a contaminated surface
- Apply waterproof membranes on a damp or wet surface
- Lack of waterproof priming
- Faulty waterproof membrane overlapping
- Improper drainage systems in the waterproofing area
- Resettlements in waterproofed structure
- High hydrostatic pressure above the waterproofing area
- Improper heating on torch membrane waterproofing systems
- Apply waterproof membranes on uneven surface
These 11 reasons cause to form cracks, fractures, gaps, blisters, and peelings on the waterproofing system. These causes increase the costs for repairs, maintenance, and replacement. In addition, waterproof membranes are subjected to more UV degradation, less flexibility, and less durability due to opening the membrane to the environment.
Therefore, these effects can reduce the effectiveness of the waterproofing membrane, reduce its adhesiveness, and increase the decay rate of the materials. Finally, as a result of the above causes waterproofing system can fail and damage the structure by leaking water inside.
The most waterproofing failures in the building are bathroom waterproofing failures, shower waterproofing failures, and basement waterproofing failures. During your waterproofing failure, standard homeowner’s insurance policies do not cover waterproofing failure damages due to a failed waterproofing system In order to protect your home from waterproofing failures, you should purchase additional coverage, like a rider or supplemental policy, to cover certain types of water damage.
You can claim a waterproofing failure warranty up to 10 years since it is installed date. You can protect a waterproofing membrane by regular maintenance, avoiding harsh chemicals, doing a professional installation, protecting against physical damages, using quality products, applying a protective layer, preparing proper drainage, maintaining proper slope and doing continuous inspections and repairs.
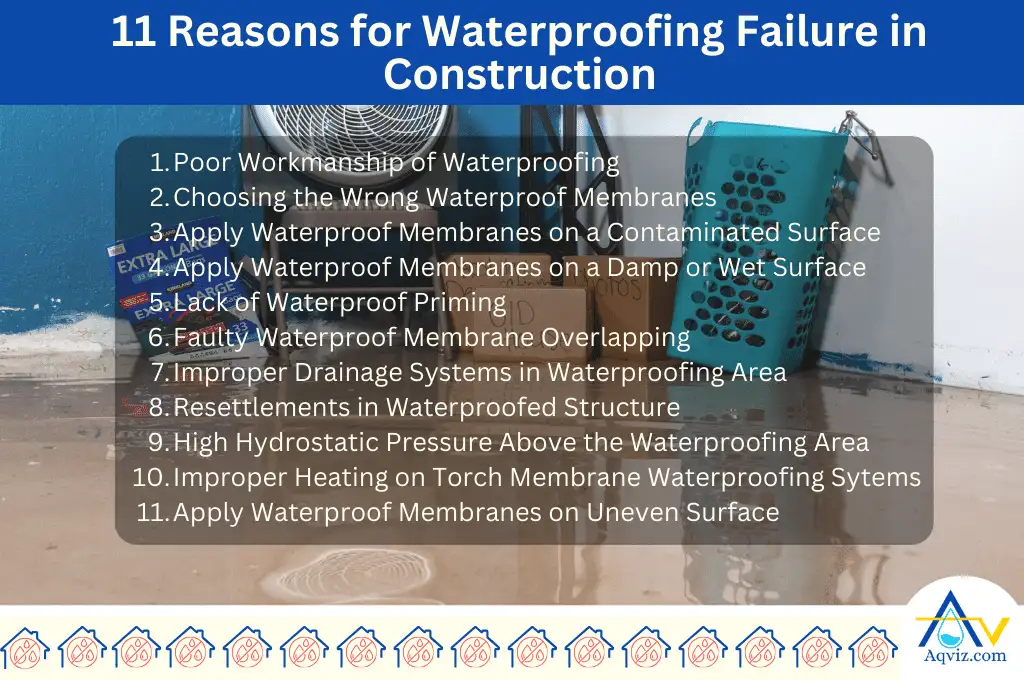
1. Poor Workmanship of Waterproofing
A waterproofing system can be failed due to poor workmanship. Poor workmanship of the waterproofing membrane is considered as not following the correct guidelines and methods statements for substrate preparation and waterproof laying.
Poor workmanship of the waterproofing installation causes quick membrane fails, increases the cost of waterproofing, reduces the service life, and increases the maintenance and repairs. Due to these failures, water can leak through the waterproofing membrane.
These are the 6 reasons for the poor workmanship of the waterproofing membrane.
- Ignoring design specification
- Inadequate surface preparation
- Incomplete substrate covering
- Incorrect waterproofing membrane installation techniques
- Lack of waterproof membrane maintenance
- Not considering the environmental effect before waterproof laying.
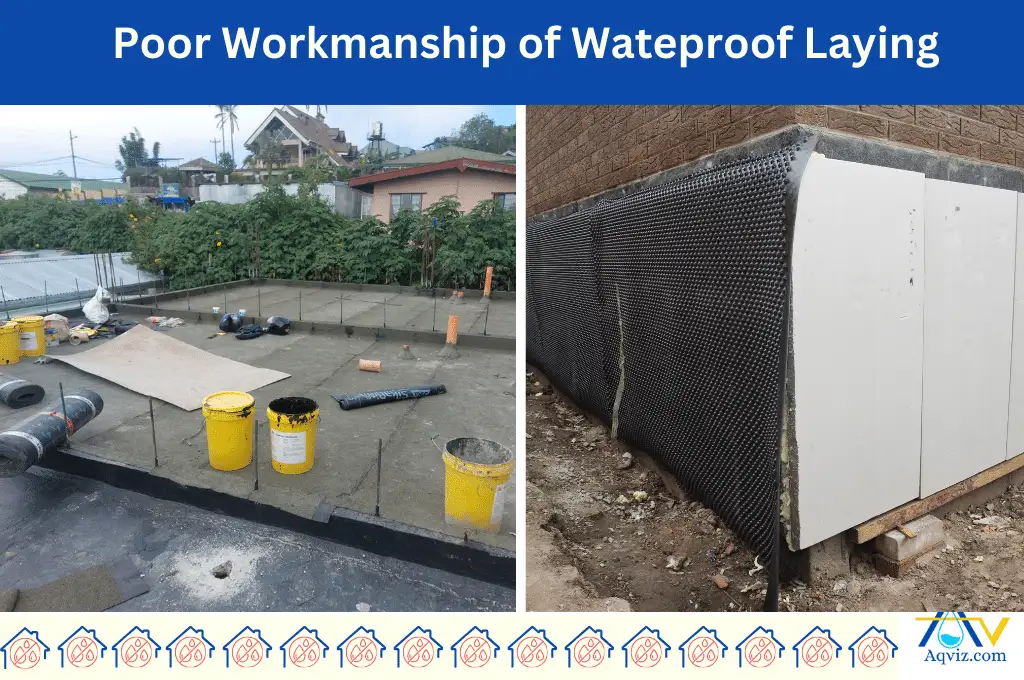
2. Choosing the Wrong Waterproof Membranes
A waterproofing membrane can fail due to choosing the wrong waterproof membrane. A wrong waterproof membrane is considered as a low quality, less adhesive, less durable, UV degradable, low budget, and weather degradable waterproof membrane as the water impervious layer.
A wrong waterproofing membrane can reduce the substrate protection due to wear and tear, making it less temperature sensitive, UV degradable, less flexible, and less durable. As a result of these failures waterproofing membrane can seep the water into the substrate.
A Wrong waterproofing membrane can be chosen due to
- Poor waterproofing skills and knowledge.
- The allocated waterproofing budget is insufficient.
- Lack of environmental and structural knowledge for waterproofing
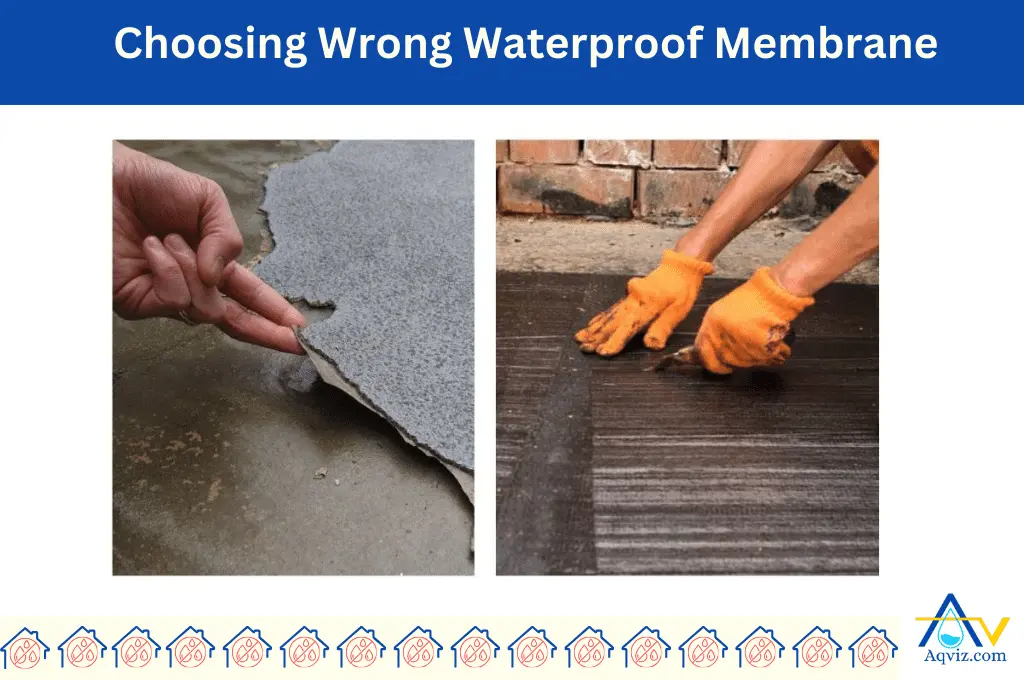
3. Apply Waterproof Membranes on a Contaminated Surface
A waterproofing membrane can fail due to application on a contaminant surface. A contaminant surface is considered as polluted, unclean, or has existing residues such as oil, grease, dust or any other particulates that could affect the bonding or adherence of the waterproofing layer to the substrate.
Applying a waterproofing membrane on a contaminant surface can reduce the bonding strength, resulting in poor adhesion and the formation of blistering and peeling over time. A contaminated surface can reduce the overall effectiveness of the waterproofing membrane. It leads to various issues like dampness, water leakage, and structural damage.
These are the 4 reasons for the application waterproofing layer on a contaminated surface.
- Improper substrate cleaning and preparation for the waterproofing membrane.
- Ignorance or lack of knowledge about the importance of a clean surface for the application of the waterproofing system.
- Speeding up the project process or overlooking crucial steps in preparing the surface for the waterproofing application.
- Poor site management and lack of regular inspection and monitoring during the application phase.
4. Apply Waterproof Membranes on a Damp or Wet Surface
A waterproofing membrane can fail due to applying a waterproofing membrane on a damp or wet surface. Applying a waterproofing membrane on a damp or wet surface means laying the membrane on areas that are not properly dried and moisture-containing.
When the waterproofing membrane is applied on a damp or wet surface, it can significantly reduce the effectiveness of the waterproofing layer. The presence of moisture can prevent the proper adhesion of the membrane to the surface, making it unable to form a successful barrier against water. This can result in water leakage, the formation of mold and mildew, and the deterioration of the building structure over time.
These are 3 reasons for applying a waterproofing membrane on a damp or wet surface.
- Lack of proper surface preparation before waterproof application.
- Weather conditions such as rain or high humidity during the waterproofing application process.
- Insufficient drying time given to a newly constructed or repaired surface before application.
5. Lack of Waterproof Priming
A waterproofing membrane can fail due to a lack of waterproof priming. Waterproof priming is a coating that is applied to the substrate before applying the main waterproofing product. Waterproof primers improve the adhesion and bonding strength of the waterproofing layer. Hence it is an essential step of the waterproofing installation process.
A lack of priming can lead to weak adhesion of the waterproofing membrane. It causes to waterproof layer peeling, blistering, or de-bonding from the substrate. This can ultimately lead to leaks and water ingress into the structure. As a result of this, we can see rotting, mold, and mildew growth on the surface.
These are the reasons for the lack of waterproofing priming.
- Limited knowledge or skill about the importance of priming in the waterproofing process.
- Ignorance of manufacturer’s instructions recommending the application of waterproof primer.
- Trying to save time or cut corners during the waterproofing process due to tight schedules.
- Budget constraints led to the omission of waterproof priming to save on material costs.
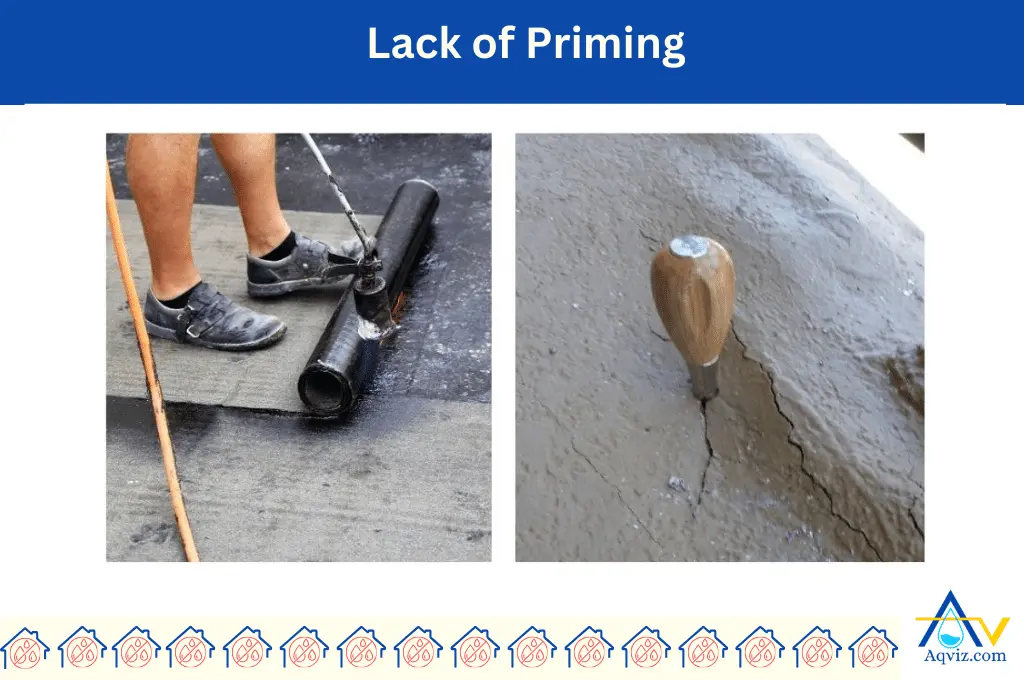
6. Faulty Waterproof Membrane Overlapping
A waterproofing layer can fail due to faulty overlaps. Faulty overlaps of the waterproofing membrane is a situation where the waterproofing layers are not correctly overlapped and connect with each other. Faulty waterproofing membranes are a huge problem in sheet membrane waterproofing. For the liquid waterproofing membrane, we should maintain the recommended waterproofing coatings in order to maintain the proper thickness and overlapping.
If the waterproofing membrane overlapping distance is not maintained properly, it causes the water to leak to the substrate. This water exposure causes a variety of issues, like dampness in the building, the growth of mold and mildew, and potential structural damage due to water ingress.
These are the most 5 common reasons for the faulty waterproof membrane overlapping.
- Improper measurement during the precutting of the waterproofing layer.
- Improper heating during the torch waterproofing membrane use.
- Inadequate training and expertise in the installation of waterproofing layers.
- Poor workmanship, where attention to detail is not given during the process.
- The use of an inappropriate or low-quality adhesive that fails to bond the overlaps properly.
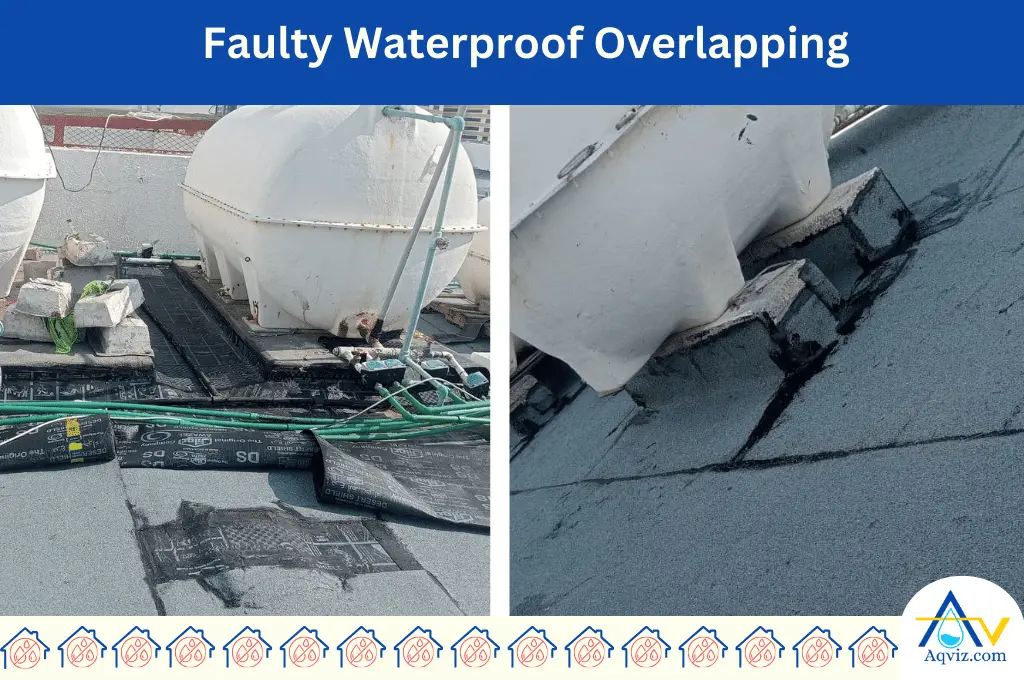
7. Improper Drainage Systems in Waterproofing Area
A waterproofing membrane can fail due to having an improper drainage system. An improper drainage system means that it does not have the capability or the capacity to properly handle and manage the flow of water due to basement and foundation seepage.
An improper drainage system can flood the area, and it reduce the waterproofing capacity of the waterproofing membrane. Hence, it tends to leak water through the layer and wear and tear. This can occur on the waterproofing membrane over time.
These are the 4 reasons for the Improper drainage system in the waterproofing system.
- Poor planning and design of the waterproofing system in the initial construction phase.
- Lack of regular maintenance and inspection of the drainage systems.
- Inefficiency in the drainage system's components, such as faulty pipes, filters, and water outlets.
- Environmental factors, such as large volumes of rain or snow, exceed the capacity of the drainage system.
8. Resettlements in Waterproofed Structure
A waterproofing membrane can fail due to the resettlements in the structure. Resettlements in the structure refer to the shifting or movement of a building or its parts due to a range of factors, such as ground movements, and geological and climatic conditions. This resettlement can lead to cracks and fractures in the substrate where the waterproofing membrane is installed.
Resettlement in a structure can significantly damage the waterproofing layer by causing cracks, fractures, or gaps, which reduces its efficiency. Therefore, water can seep through the cracked and damaged substrate, reduce the structural strength and damage the walls, ceiling, and walls.
Resettlements in a structure causing waterproofing failures can occur due to:
- Geological or ground movements causing structural shifts.
- Climatic conditions such as extreme temperature changes result in the expansion and contraction of materials.
- Inferior construction techniques lead to unstable and weak structures.
- Aging of the building materials leads to reduced strength and resilience.
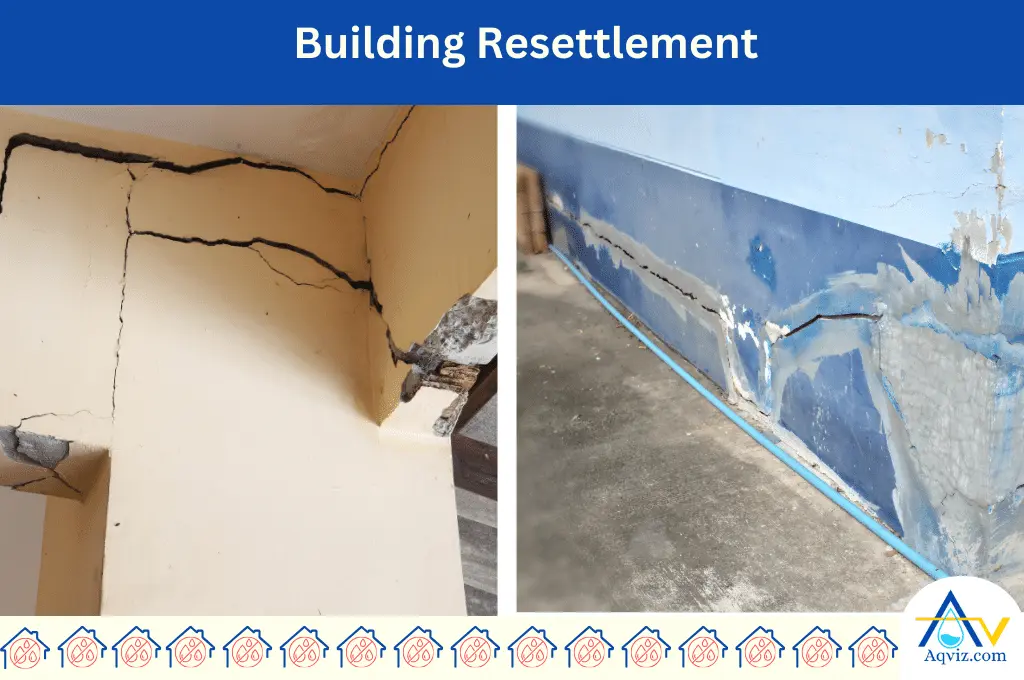
9. High Hydrostatic Pressure Above the Waterproofing Area
A waterproofing layer can fail due to high hydrostatic pressure above the waterproofing area. High hydrostatic pressure is a force exerted by water that increases with depth. When a higher hydrostatic pressure is increased around the basement or foundation, it can reduce the bonding strength between the waterproofing layer and substrate. As a result of this, it can damage the waterproofing membrane.
High hydrostatic pressure can lead to cracks and leaks in the waterproofing layer. As the pressure builds, it can push the waterproofing membrane away from the substrate. It leads to failure points that allow water to seep into the building. These kinds of pressure increments can not be controlled by the interior waterproofing membrane. You have to use the exterior waterproofing membrane and drainage system before applying the waterproofing on the substrate.
These are the reasons for increasing higher hydrostatic pressure around the waterproofing area.
- The groundwater level is increased around the waterproofing area.
- Poor drainage system around the waterproofing area or existing drainage system is blocked.
- Soil condition around the waterproofing area.
10. Improper Heating on Torch Membrane Waterproofing Sytems
A waterproofing membrane can fail due to Improper heating on the torch membrane waterproofing system. Torch membrane waterproofing such as bituminous and PVC sheet membranes should be heated more than 40 degrees Celsius of heat as it allows to adhere properly to the surface. If the heating is not applied appropriately, it can lead to failure in the membrane's adhesion, resulting in inadequate waterproofing.
Improper heating on torch membrane waterproofing causes an incomplete bond between the membrane and the surface. As a result of this, we can see holes and blisters in the waterproofing layer. Hence, this can result in structural damages due to water leaking and reduce the life expectancy of the system, requiring additional costs for early replacement and repair.
These are the 3 reasons for improper heating on the torch membrane.
- Lack of understanding of torch waterproofing membrane installing
- Insufficient or inadequate equipment for waterproof membrane heating.
- Wrongly estimated time for heating, leading to either over or under-heating.
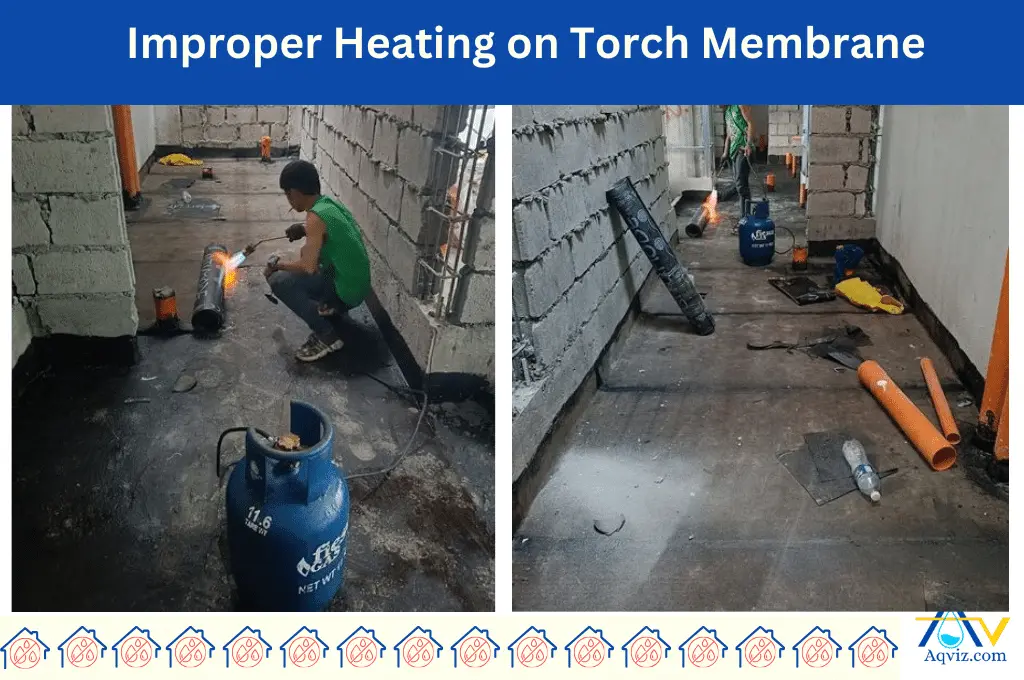
11. Apply Waterproof Membranes on Uneven Surface
A waterproofing membrane can fail due to applied on uneven surfaces. An uneven surface is considered as a waterproofing substrate that is not smooth, flat, or level but instead has bumps, ridges, holes, or depressions.
Applying a waterproofing membrane on an uneven surface can prevent it from adhering properly and might create air pockets or voids that can allow water to penetrate underneath. This can lead to the detachment of the membrane. This can affect its longevity and effectiveness. Over time, this could result in water leaks or seepages and, eventually, cause to structural damage.
These are the 4 reasons for applying waterproofing membranes on uneven surfaces.
- Poor waterproofing surface preparation
- Use of inappropriate application tools or methods for waterproof surface preparation
- Lack of adequate training or skill for waterproofing.
- Ignoring manufacturer's instructions on surface preparation for waterproofing.
What are the Common 3 Waterproofing Faulires in a Building?
The common 3 waterproofing failures in the building are bathroom waterproofing failures, shower waterproofing failures, and basement waterproofing failures. These are the most water engaged building components. Hence most of waterproofing failures and effects can be seen in these areas.
Read more: Building Waterproofing: What you Should Know?
Bathroom Waterproofing Failure
Bathroom waterproofing failure is leaking or seeping water through the installed waterproofing layer in the bathroom. Bathroom waterproofing failure can occur on the bathroom floor, walls and ceiling. This can happen due to selecting poor quality materials, structural movements, using harsh chemicals, incorrect membrane installation, inadequate surface preparation and poor workmanship for the waterproofing installation.
Bathroom waterproofing failure causes to structural, wall, and floor damage due to water seepage, dampness on the walls, and growing mold and mildew on the surface. As a result of this, It can reduce the structural strength and aesthetic view of the bathroom by peeling paint, unsightly discoloration, or damaged flooring.
Shower Waterproofing Failure
Shower waterproofing failure is leaking water from the bathroom shower walls due to shower wall waterproofing layer damage. The shower wall waterproofing layer can be damaged due to the selection of poor quality materials, structural movements, the use of harsh chemicals, incorrect membrane installation, inadequate surface preparation, and poor workmanship for the waterproofing installation.
A waterproofing failed showering area lets water seep into the structure. Seeped water can reduce the structural strength and aesthetic view of the walls.
Basement Waterproofing Failure
Basement waterproofing failure is damaging the installed waterproofing layer on the basement floor and walls. The basement waterproofing layer can be damaged due to structural stability fluctuations, higher hydrostatic pressure, selecting the wrong waterproofing membranes, lack of drainage system, avoiding exterior waterproofing, and poor workmanship.
Basement waterproofing failure causes to reduce structural strength, increased mold and mildew growth, peeling and blistering of the paints, and flooding of the basement.
Does Homeowners Insurance Cover Waterproofing Failures?
Standard homeowner’s insurance policies do not cover waterproofing failure damages due to a failed waterproofing system. But homeowners insurance covers sudden and accidental water damage, such as burst pipes or overflow, but not for continuous water damage. This falls under the responsibility of the homeowner's regular home maintenance duties.
In order to protect your home from waterproofing failures, you should purchase additional coverage, like a rider or supplemental policy, to cover certain types of water damage. It's also worth noting that while the damage caused by the failure of waterproofing may not be covered, the source of the water causing the damage may be. For instance, if heavy rain leads to flooding that your system failed to handle, you may have some level of coverage if you have flood insurance.
How Long can I have a Waterproofing Failure Warranty?
You can claim a waterproofing failure warranty up to 10 years since it is installed date. Waterproofing warranties are two types. Fully covered and partially covered. In the fully covered warranty, you are covered for both labor and materials. In the partially covered waterproofing warranty, you have to provide the material, and the service provider will provide the skilled labor for you.
How to Protect Waterproofing Membranes?
A waterproofing membrane can be protected by regular maintenance, avoiding harsh chemicals, doing a professional installation, protecting against physical damages, using quality products, applying a protective layer, preparing proper drainage, maintaining proper slope and doing continuous inspections and repairs.
- Regular maintenance and inspection on waterproofing membrane
- Avoid using harsh chemicals on the waterproofing layer
- Do professional waterproofing installation
- Protect waterproofing membrane against physical damage
- Use quality waterproofing products
- Install protective layers on the waterproofing membrane
- Use UV-protective waterproof membranes
- Proper drainage around the waterproofing area
- Maintain the correct slope on the waterproofing substrate