Epoxy Crack Injection: Uses, Properties, Applications, and Troubleshooting
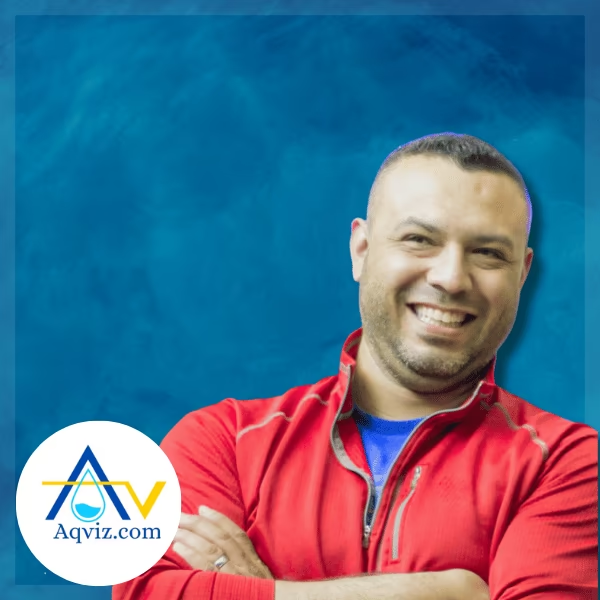
Epoxy crack injection is a crack sealing process by injecting epoxy grout into the cracks in concrete, wood, bricks, stones, fiberglass, ceramics and composite materials. The epoxy crack injection method can be used in building and residential structures, tunnels and underground structures, and marine and coastal structures.
Epoxy crack injection is cost-effective and offers higher water resistance. It is versatile, withstands a wide range of environmental conditions, and has strong adhesion properties. Additionally, it is durable, long-lasting, and easy to maintain.
Epoxy injection consists of different chemicals such as epoxy resin and hardener, surface preparation solvents, injection port adhesive, anti foaming agents and thixotropic agents. All of these materials help the epoxy sealant flow smoothly through the crack.
When you use epoxy crack injection, it can cure between 3-24 hours and withstand more than 10-15 years. The effective width for the epoxy crack injection is 0.25mm to 3.2mm. Epoxy crack injection is not fire resistant due to carbon based organic compounds in the epoxy mixture.
Epoxy crack injection requires special tools such as injection ports, injection pumps, and stir sticks rather than regular cleaning and surface preparation tools for waterproofing.
When you inject the epoxy into the cracks, you should first prepare the surface. Then, injection ports are installed, and the surface is sealed to cover the entire cracking path. Then, mix the epoxy resin and inject the epoxy from the lowest point of the crack. You should repeat the process until no more ports accept epoxy. You should monitor the flows and wait until all ports are filled completely. Then, allow the epoxy to cure and remove the ports by cutting them and sanding the surface smoothly.
If the injected epoxy is damaged you can repair it using a new epoxy layer by applying a new layer on the existing epoxy substrate.
If the back pressure prevents epoxy injection, you should stop the injection process and check the back pressure source, clean the crack to remove destructions, properly install the ports and widen the narrow sections to penetrate effectively.
If more epoxy is used than your estimation, it can be due to cracks expanding; epoxy is running out of the backside, internal voids or cavities, and the substrate is more porous.
If less epoxy is used than your estimation, it can be due to shallow cracks, improper mixing, inadequate injecting process and epoxy is not penetrate the entire length of the crack.
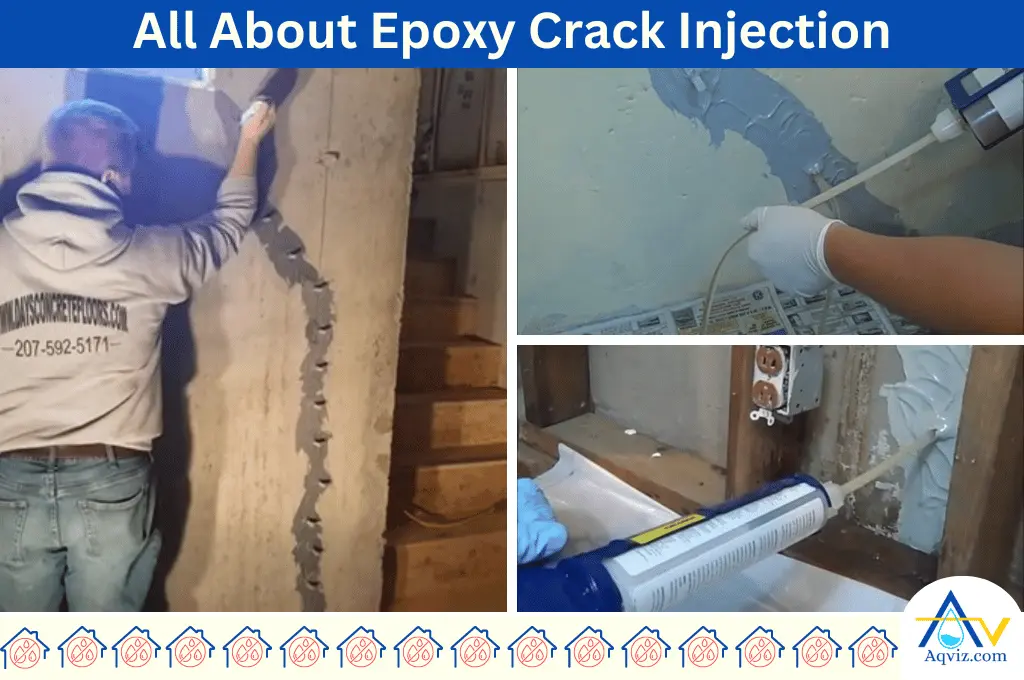
What is Epoxy Crack Injection?
Epoxy crack injection is the process of repairing cracks in concrete structures by injecting epoxy in to the crack paths. Epoxy crack injection is mostly used in deeper level cracks like in thick walls, slabs, and foundations, rather than in shallow surface level cracks.
Epoxy can be injected into concrete cracks where in buildings and residential structures, tunnels and underground structures, and in marine and coastal structures. Injecting epoxy into the cracks can bond the fractured concrete, restore its structural integrity, be adaptable to a wide range of environmental conditions, cost effective, and easy maintenance.
Epoxy crack injection is completely different from the epoxy waterproofing. Epoxy waterproofing is a waterproofing method that is used to seal the surface instead of injecting it inside the material.
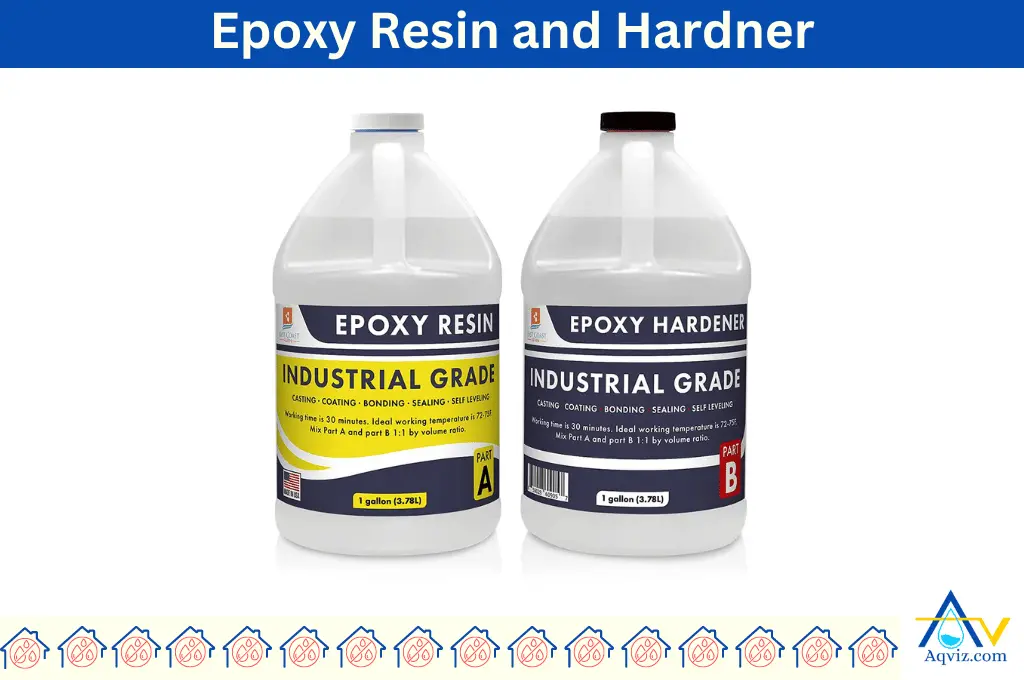
How Long Does It Take to Cure Epoxy Crack Injection?
The epoxy crack injection will take approximately 3-24 hours at room temperature after it is injected into the cracking path. You should not expose the injected site to water, moisture, or any chemicals, subject the repair area to any vibrations, skip the epoxy manufacturer’s instructions, and ignore safety precautions.
How Long Does an Epoxy Crack Injection Last?
The epoxy crack injection can last long between 10 to 15 years if it is properly maintained and repaired. You can improve this durability period with best performance by maintaining regularly, using high quality epoxy, correctly mixing the epoxy and the hardener to precise ratios, using proper injecting techniques, and using the recommended temperature range for the epoxy resin.
Where Can You Use Epoxy Crack Injection?
Epoxy crack injection can be used on foundation cracks, water tanks and pools, tunnels and bridges, transportation infrastructure, and in marine and coastal structures.
- Foundation crack sealing : Epoxy crack injection can be used to seal the foundation crack in foundation waterproofing. Epoxy crack injection on the foundation helps to restore the structural integrity of the foundation, prevents moisture from entering the foundation, and provides a long-lasting repair that can withstand different environmental conditions.
- Water tanks and pools : Epoxy crack injection can be used on water features for water tank waterproofing and swimming pools. Epoxy crack injection on water structures prevents leakage of water, maintains water quality, prevents contamination and maintains operational efficiency.
- Tunnel and bridges : Epoxy crack injection can be used to treat cracks in tunnels and bridges due to waterproofing. Epoxy crack injection on tunnels and bridges helps to maintain structural stability and prevent water penetration and corrosion of metals like steel.
- Transportation infrastructure : Epoxy crack injection can be used on cracks in airport runways and railway tracks for waterproofing. Epoxy crack injection ensures safe landings and takeoffs, prevent water infiltration and track deterioration.
- Marine and coastal structures : Epoxy crack injection can be used for waterproof piers and wharfs which are exposed to seawater. Epoxy crack injection prevents corrosion of these structures and prevents structural failure.
Can I Inject Epoxy Into Wet and Leaking Cracks?
Yes, you can inject epoxy into wet and leaking cracks in the concrete because it shows excellent resistance to moisture and water. It offers long term durability, which prevents water infiltration, and is an immediate waterproofing solution for sealing leaking cracks.
What Material Can You Inject Epoxy?
You can inject Epoxy into below 7 materials
- Concrete
- Wood
- Masonry (brick and stone)
- Steel
- Fiberglass
- Ceramics
- Composite materials
Is Epoxy Crack Injection Fire Resistant?
No, epoxy crack injection is not fire resistant. Because epoxy crack injection contains carbon based organic compounds which are highly flammable, epoxy resins can burn and degrade when exposed to higher temperatures or direct flame, and epoxy resins do not contain fire-retardant additives that can improve their resistance to fire.
What Are the Advantages of Epoxy Crack Injection?
Given below are 6 advantages of epoxy crack injection.
- Cost-effectiveness
- Effective in waterproofing
- Adaptable to a wide range of environmental conditions
- Strong adhesion property
- Durable and a long-lasting solution
- Versatility, used on a broad range of applications.
How To Do Epoxy Crack Injection?
These are the 8 steps of Epoxy crack injection
- Surface preparation: Remove dirt and clean the crack surface using a wire brush or compressed air. Make sure the area is dry before starting the epoxy crack injection.
- Install injection ports: Set the injection ports along the length of the crack, typically 6-12 inches apart. Then, secure the ports with epoxy paste or adhesive.
- Seal the surface: Apply epoxy paste or gel on the cracked surface. Ensure that the cracked surface is entirely covered to prevent epoxy leakage during the injecting process.
- Mix epoxy resin: Carefully mix epoxy resin and hardener to a 2 to 1 ratio. Ensure accurate proportions and a thorough mixing.
- Inject epoxy: First, begin injecting the epoxy to the lowest port and continue until it reaches to the adjacent port. When this happens, seal the initial port and move to the next port. Repeat the process until no more ports are accepting epoxy.
- Monitor flow: Monitor the flow of epoxy during the injecting process to make sure make sure the ports are completely filled. Do not rush this step; allow sufficient time for the epoxy to penetrate deeply.
- Allow Curing: Let the epoxy cure and harden for the recommended time. The time varies on the epoxy product used and environmental conditions. Do not apply any load to the repaired area during this period.
- Remove ports and surface sealant: After curing, when the area is completely dried, remove the injection ports by cutting them in a straight line to the surface. Then, sand and smooth the epoxy surface and apply a finishing coat if desired.
What Tools Need for Epoxy Crack Injection?
Following are a list of tools that are needed for epoxy crack injection.
- Wire Brush
- Compressed Air Blower or Vacuum
- Injection Ports
- Epoxy paste or gel
- Injection Pump
- Mixing Cups
- Stir sticks
- Cutting tools
- Sandpaper
- Cleaning solvents
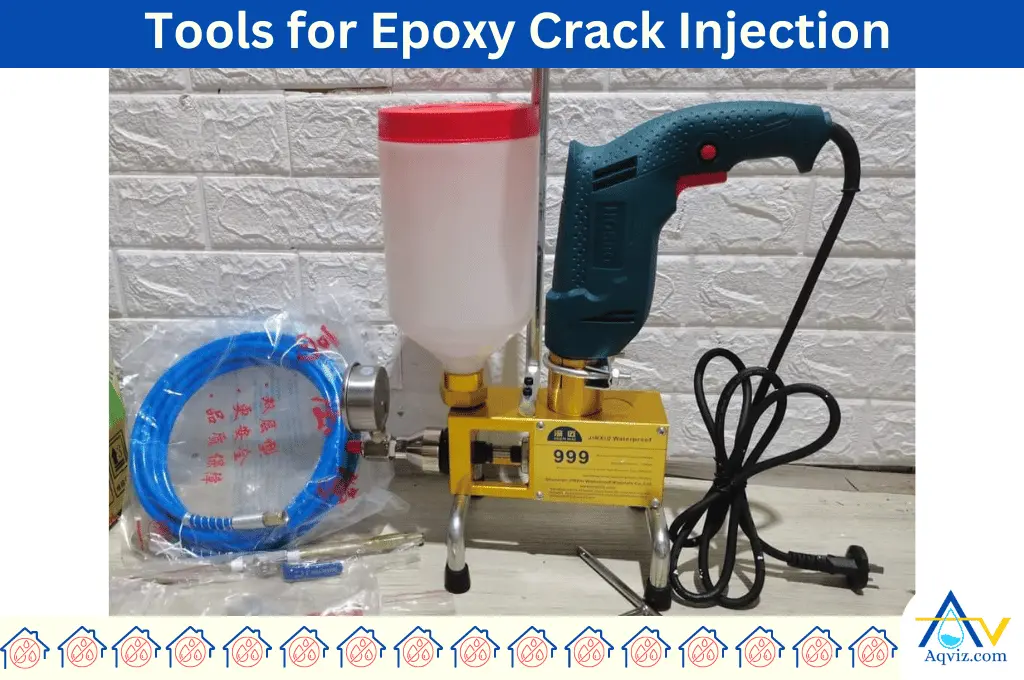
What Chemicals Need for Epoxy Crack Injection?
The 6 chemicals for epoxy crack injection are epoxy resin and hardener, surface preparation solvents, epoxy paste and gel, injection ports adhesive, anti-foaming agents, and thixotropic agents.
- Epoxy Resin and Hardener : The resin and hardener mix to form a strong bond. This solution is the prime solution that is injected into cracks to seal and reinforce them.
- Surface preparation solvents : Preparation solvents like acetone isopropyl alcohol clean the cracked surface, removing the contaminants that can disturb the adhesion of the epoxy.
- Epoxy paste or gel : Epoxy paste or gel is used to seal the cracked surface and secure injection ports. Sealing the surface will prevent leakage during the injection of epoxy.
- Injection Ports Adhesive : Injection ports adhesive is used to secure the injecting ports in place. The epoxy paste or gel used in the sealing process can also be used for this purpose as well.
- Anti-foaming agents : Anti-foaming agents prevent the formation of air bubbles in the epoxy mixture. Anti-foaming agents ensure a smooth injecting process.
- Thixotropic Agents : Thixotropic agents adjust the viscosity of the epoxy mixture to prevent it from sagging or flowing out of overhead cracks before it cures.
What Size Cracks Can Be Fixed by Epoxy Crack Injection?
You can use epoxy crack injection on a minimum width of 0.05mm and a maximum width of 6.35mm. The effective width for the epoxy crack injection is 0.25mm to 3.2mm.
When you inject epoxy to the optimum width, it can be efficient in sealing and provide a strong bond, and it maintains and restores the structural integrity of the concrete. Therefore, using the right width is worth it because it prolongs the lifespan of the structure.
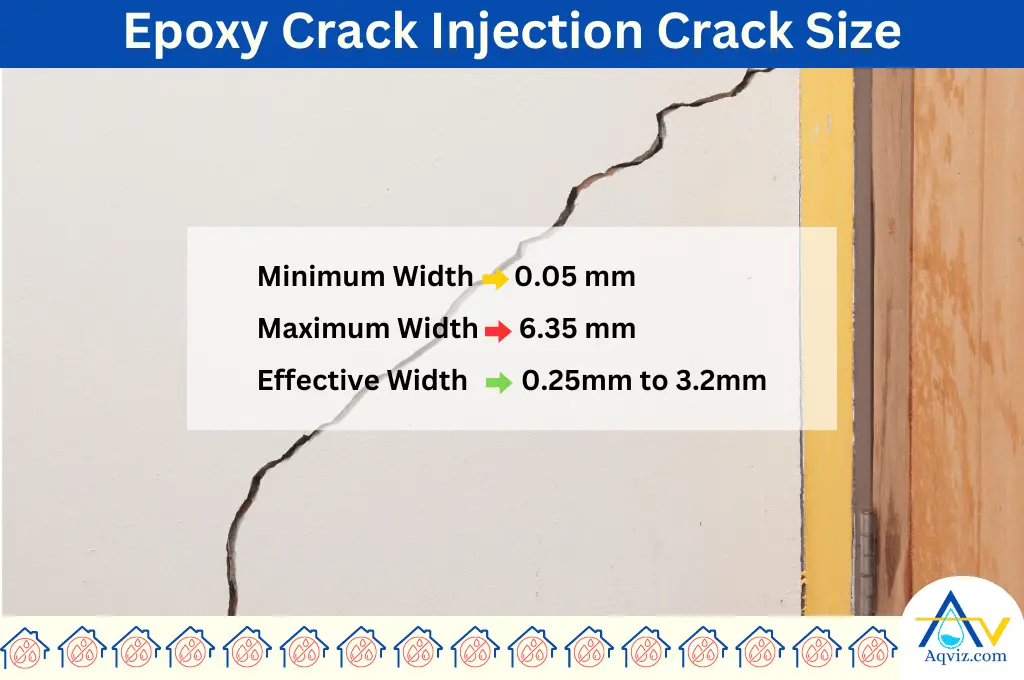
How Do You Stop Injecting Epoxy from Running the Port?
You should follow below 6 steps to prevent epoxy from running out of the injection ports during the crack injection process, you can follow the below steps.
- Clean the crack area properly
- Install injection ports 6-12 inches apart along the crack, firmly securing the ports to avoid any movement during the injecting process.
- Apply a high-quality, fast curing epoxy paste to seal the entire surface around.
- Inject epoxy at low pressure starting from the lowest point, and close each port after injection to prevent backflow.
- Monitor for any signs of leakage, if a leak occurs, stop injecting and re-seal the area before resuming.
- Allow the epoxy for a sufficient curing time according to the manufacturer’s instructions.
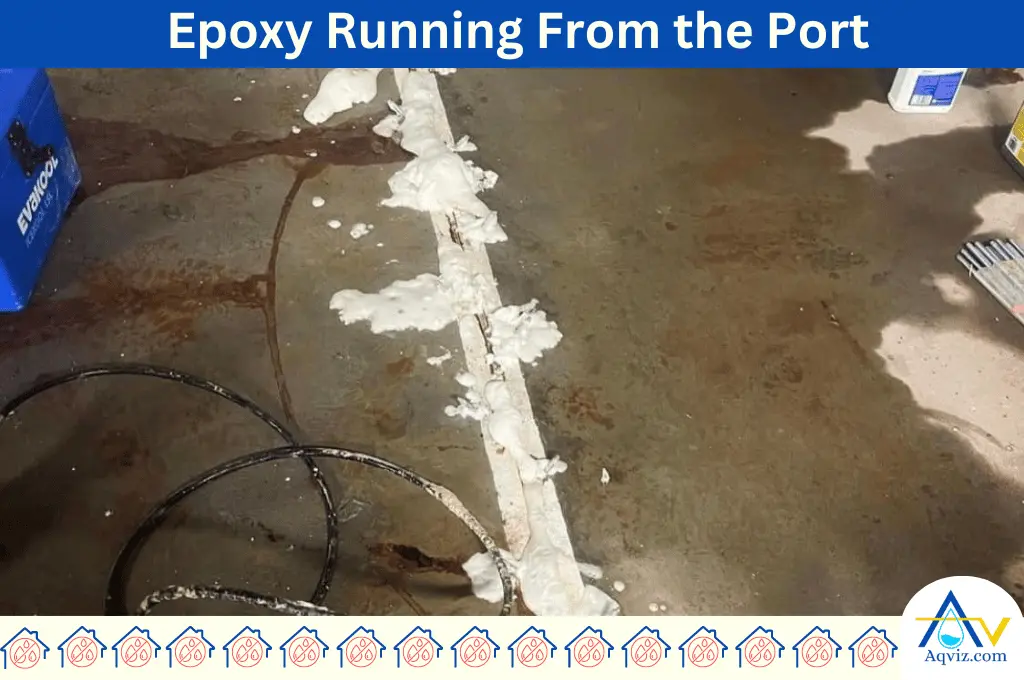
What If an Inject Epoxy Leak?
If an epoxy injection leaks, you should follow the steps below.
- Stop the epoxy injection: Immediately halt the epoxy injecting process to prevent further leakage and wastage of epoxy
- Identify the source of leakage: Inspect the area around the crack and injection ports to locate the exact source of the leak
- Seal the epoxy leak: Clean the area around the leak and thoroughly re-seal the area using a quick-setting epoxy paste.
- Re-check injection ports: Check the injection ports are properly installed. Tighten or reposition the ports as necessary.
- Reinforce the surface seal: Apply an additional layer of surface sealant over the cracked surface to prevent future leaks.
- Allow the sealant to cure: Wait for the sealant to fully cure according to the manufacturer’s instructions before resuming the injection process.
Can You Repair the Epoxy Crack Injection?
Yes, you can repair epoxy crack injection paths on the material when it gets re cracked or damaged due to any reasons. You can restore the structural reinforcement by injecting epoxy back again to the repaired area. Injected epoxy can be highly adhesive to the old epoxy substrate and bond permanently by creating a seamless repair.
The epoxy crack injection helps to prevent water infiltration, the repair process is quick, cost effective than other large scale structural repairs, and maintains the structural integrity of the cracked area.
What If Back Pressure Prevents Epoxy Injection?
If back pressure prevents epoxy injection, you should follow the below 4 solutions
- Stop the injection process and identify the source of the back pressure.
- Clean the crack thoroughly if there is any obstruction disturbing the crack.
- Ensure that the injection ports are properly installed and there is enough room for air and excess epoxy.
- Widen narrow sections to ensure epoxy can penetrate effectively.
These are 4 the issues if the back pressure prevents epoxy injection.
- The crack is blocked by debris.
- The injection port is not properly aligned over the crack.
- The injection epoxy used has a higher viscosity
- Insufficient venting or the crack is not continuous, and the portion being injected is full.
What If More Epoxy is Being Used Than Estimated?
If more Epoxy is being used than estimated, you should follow the below 4 solutions.
- Inspect and seal the leaks.
- Re-evaluate the crack size and adjust the epoxy quantity.
- Identify and fill any internal voids and cavities in the crack
- Apply a primer or an initial sealing coat to a porous substrate.
These are 4 issues if more epoxy is being used than estimated.
- Crack either expands or branches off below the surface
- The epoxy is running out of the backside of the crack
- Internal voids or cavities that consume more epoxy
- The concrete or substrate is more porous.
What If Less Epoxy is Being Used Than Estimated?
If less Epoxy is being used than estimated, you should follow the below 4 solutions.
- Monitor the injection process to ensure that it fills the entire crack length.
- Ensure that the epoxy resin and hardener are mixed in the proper ratio.
- Inspect the crack area to ensure that there are no blockages.
- Heat the epoxy to 80-100 degrees Fahrenheit to reduce the viscosity of the epoxy and allow it to penetrate through smaller cracks.
These are 4 issues if less epoxy is being used than estimated.
- The crack can be shallowed than expected.
- Improper mixing of epoxy resin and hardener
- Inadequate injection process.
- Epoxy is not penetrate the entire length of the crack.
Is Polyurethane Injecting Better Than Epoxy Injecting?
Polyurethane waterproofing is better than epoxy injection when the substrate is in wet condition, needs to fill larger and irregular shape cracks, and needs to seal wet or actively leaking cracks.