Flat Roof Waterproofing: Tools, Guide, Mistakes, Maintenance
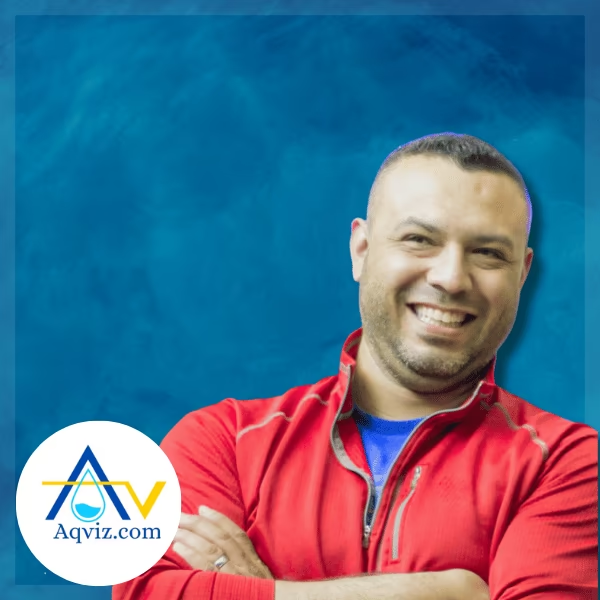
A flat roof is a horizontal or nearly level roof design that typically features a slight pitch. A flat roof has a 10-degree slope or 1/4 to 1/2 inch per foot for proper drainage over the surface. During the rain or snow season, water does not drain well due to the flat surface. Hence, water can be leaked through the roof during this period. In order to prevent water from leaking, flat roofs should be waterproofed properly.
Flat roof waterproofing can be done by using a coating or membrane. Among these, sheet membrane waterproofing is the most successful waterproofing method for flat roofs. Flat roof waterproofing requires professional experience for substrate preparation and membrane laying. As waterproofing experts, we do not recommend doing it DIY for large surfaces, but for small surfaces. When you waterproof a flat roof, you should follow these 9 steps.
9 Steps to waterproof a flat roof.
- Inspect the flat roof
- Clean the flat roof surface
- Repair any damage on flat roof
- Choose a waterproofing method
- Apply waterproofing material on the flat roof
- Seal seams and edges
- Allow proper curing time
- Conduct a final inspection
- Maintain the flat roof regularly
More than that, you should have the essential tools that our experts have mentioned in this guide. A flat roof waterproofing can be damaged if you skip the surface cleaning, ignoring all cracks, using incompatible materials, improperly seam sealing, applying coating in wet or cold conditions, and lack of maintenance and inspection after installation.
In order to have an efficient flat roof, it should be maintained properly. As well as you should fix all the rising problems on the surface after the waterproofing. Else, you can see leaks on the flat roofs, and it can lead to heavy water damage if it is not addressed on time.
How to Waterproof a Flat Roof?
These are the 9 Steps to waterproof a flat roof.
- Inspect the flat roof
- Clean the flat roof surface
- Repair any damage on the flat roof
- Choose a waterproofing method
- Apply waterproofing material on the flat roof
- Seal seams and edges
- Allow proper curing time
- Conduct a final inspection
- Maintain the flat roof regularly
1. Inspect The Flat Roof
As the first step of flat roof waterproofing, you should always begin with a thorough roof inspection. You should look for visible cracks, ponding water, punctures, deteriorated flashing, or blistering on the roof. In order to check invisible water damage, you should use a digital moisture meter and an infrared thermometer gun to detect hidden damp spots and thermal bridging. And also you should check around roof penetrations, seams, HVAC units, and drains on the roof.
If you observe any structural damage, such as sagging or rotted decking, it must be addressed before waterproofing begins. This diagnostic step helps to determine the most suitable waterproofing system, whether it’s liquid-applied membranes or torch-on bitumen.
Before you start flat roof waterproofing, you should know this guide: What You Should Know About Roof Waterproofing.

2. Clean The Flat Roof Surface
Once inspection is complete, you should pressure wash the entire surface using a pressure washer to remove dirt, algae, moss, and loose particles. For corners and seams, we use roof brooms and stiff brushes for detail work.
Cleaned roof surface ensures proper adhesion of primers, coatings, or membranes. A dry, dust-free surface improves bonding performance and extends membrane lifespan. You should always allow the surface to fully dry before applying any waterproofing materials, especially in cooler climates or shaded areas.
3. Repair Any Damage On Flat Roof
Before applying roof waterproofing, you should fix all identified issues using tools like a utility knife, roofing hammer, and caulking gun. Small punctures or membrane splits are patched with compatible repair kits or cold-applied bitumen. Flashing is resealed or replaced using flashing crimping pliers and sealant to prevent future seepage.
You should ensure all drainage paths, including internal drains and scuppers, are cleared of debris using roof brooms and a hose to avoid water pooling, which leads to membrane failure over time.
Read More About: Top 11 Roof Damages and How to Prevent Them?

4. Choose A Waterproofing Method
Selecting the right waterproofing system depends on roof slope, usage, and climate. For quick applications with minimal disruption on the roof, we often use liquid-applied coatings like polyurethane or acrylic, applied with a notched trowel and silicone roller. For heavy-duty durability, especially in commercial settings, bitumen membranes (SBS or APP) are torch-applied using a roofing torch. In heat-sensitive buildings, single-ply membranes like EPDM, TPO, or PVC are ideal.
5. Apply Waterproofing Material On The Flat Roof
You should apply the selected waterproofing method on the roof properly.
For liquid-applied roofing membranes like polyurethane or elastomeric coatings, you can use rollers, squeegees, and notched trowels to spread the material evenly at 1.5 to 2.5 mm thickness, ensuring full coverage especially around penetrations.
On bituminous roofing systems, we use a roofing torch to heat the underside of the APP/SBS membrane while unrolling it slowly, bonding it to the substrate. For EPDM or TPO, we position the sheets precisely and use adhesive and seam rollers to fix them in place, avoiding wrinkles that can trap moisture.
Read More:

6. Seal Seams And Edges
You should seal seams and edges properly to prevent leaks from the roofing membrane. On torch-on membranes, you should use a hand-held seam roller to eliminate air pockets and ensure adhesion.
For PVC and TPO roofing systems, seams are fused using a hot air welder and tested with a seam probe tool for integrity.
You should pay close attention to penetrations like vents, drains, and HVAC units, sealing them with bitumen or polyurethane sealant and reinforcing with pre-formed flashing boots. Edges are terminated using metal flashing and secured with fasteners and sealant to withstand wind uplift and water intrusion.

7. Allow Proper Curing Time
Once the waterproofing material is applied, you should always allow sufficient curing time as per the manufacturer’s specifications. For liquid-applied membranes, this ranges from 24 to 72 hours depending on product type, humidity, and ambient temperature. For example, polyurethane coatings typically cure within 48 hours at 25°C (77°F) with 50% relative humidity.
Hence, you should ensure the area remains undisturbed during this time by blocking access and monitoring the weather conditions. Premature foot traffic or exposure to rain can compromise the membrane’s adhesion and flexibility, leading to early failure.
8. Conduct A Final Inspection
After curing, you should conduct a final check using a digital moisture meter and seam probe tool to ensure full coverage and bonding. You should inspect for any missed seams, thin areas, or pooling, especially around transitions, drains, and roof edges. Then you should conduct a controlled water test if possible, flooding the roof area for 24 hours to confirm watertightness.
9. Maintain The Flat Roof Regularly
After the final inspection roofing is ready for use. You should maintain it properly. At Aqviz, we recommend bi-annual inspections using a checklist and tools like a moisture meter, broom, and ladder with stabilizers. Clean off leaves, debris, and sediment to keep drains clear. Re-seal flashing, seams, and joints every 3 to 5 years, depending on climate and wear. Early detection of hairline cracks or coating wear can prevent costly damage to the roof.
What Tools are Needed for Flat Roof Waterproofing?
Aqviz, we highly recommend that you to have tools related to these categories, such as heat application and welding tools, cutting and trimming tools, application and sealing tools, measuring and inspection tools, safety equipment, and fastening tools. Selecting these tools depends on the roofing type, roof type, shingles, and structural condition.
- Roofing torch
- Propane tank with hose
- Heavy-duty utility knife
- Notched trowel
- Silicone roller
- Squeegee
- Bitumen brush
- Hot air welder
- Digital moisture meter
- Infrared thermometer gun
- Caulking gun
- Cordless drill
- Pressure washer
- Roof brooms and stiff brushes
- Ladder with stabilizer
- Protective gloves and goggles
- Safety harness and roof anchors
- Heat-resistant boots
- Measuring tape and chalk line
- Hand-held seam roller
- Seam probe tool
- Bucket and mixing paddle
- Roofing hammer
- Roofing membrane cutter
- Flashing crimping pliers
What Are The Common Flat Roof Waterproofing Mistakes?
When you conduct a flat roof waterproofing project, these 6 mistakes can occur.
- Skip surface cleaning: Skipping surface cleaning causes to prevents proper membrane adhesion, leading to early peeling and water ingress on the roofing.
- Ignoring small cracks or ponding: Minor defects and small cracks can expand over time and cause roof membrane failure or structural rot over time.
- Using incompatible materials: Using incompatible roofing material results in chemical reactions or poor bonding. It can reduce the waterproofing lifespan.
- Improper seam sealing: Improper seam sealing causes leaks at roofing overlaps and penetrations, especially during freeze-thaw cycles.
- Applying coatings in wet or cold conditions: Applying coatings in wet or cold conditions in roof waterproofing leads to blistering, poor curing, and reduced waterproof performance.
- Lack of maintenance inspections: Improper roof waterproofing maintenance allows unnoticed damage to escalate. It causes to increase the long-term repair costs over time.
How To Maintain a Waterproof Flat Roof?
You should follow below 6 steps to maintain a waterproof flat roof.
- Inspect the roof twice a year
- Clean debris and standing water
- Check and clear roof drains
- Reseal flashings and joints
- Recoat the membrane as needed
- Hire professional inspections
How Do You Troubleshoot Common Flat Roof Waterproofing Issues?
Common flat roof problems like ponding water, blisterings or bubbles, seam failures, cracks, moss or algae growth, and membrane shrinkage can be troubleshooted as follows.
- Ponding water: Flat roofs often develop low spots where water collects. We recommend improving drainage by adding tapered insulation or scupper extensions. Persistent ponding weakens membranes like modified bitumen and acrylics over time.
- Blisters or bubbles: Roof blisters and bubbles are caused by trapped moisture or poor adhesion. We cut and patch affected areas using compatible membrane patches or reapply liquid coatings after drying the substrate fully.
- Seam failure: If seams begin to lift or separate, especially on EPDM or PVC systems, we use heat welding or patch kits to reseal them. Seam probe tools help identify weak points during routine checks.
- Cracked or degraded flashing: Flashings around vents, walls, and HVAC curbs tend to crack due to UV or movement. We seal it with polyurethane mastic or replace it with flashing tape to prevent edge leaks.
- Moss or algae growth: These hold moisture against the membrane, accelerating deterioration. Use a soft brush and roof-safe cleaner to remove growth and apply biocidal coatings if needed.
- Membrane shrinkage or tearing: Common in older EPDM roofs, shrinkage causes pulling at corners and edges. We reinforce stressed areas with cover strips and mechanical fasteners to prevent further tearing.
More than that you can see roof aligatoring, ceiling cracks, and ceiling mold in the flat roofs. You should address them asap once you observe them.
What are the Reasons for a Flat Roof Leaking?
These are the 7 reasons for flat roofing leaking.
- Poor roof drainage design
- Aging roof waterproof membrane
- Improper roof flashing installation
- Seam failure on roof waterproofing membranes
- Punctures from foot traffic
- Clogged drains or scuppers
- Incorrect roofing material
Read More About: How To Stop a Roof Leak In 9 Steps?
Is Roof Waterproofing And Insulation the Same?
No, roof waterproofing and insulation are not the same. They serve different purposes and use different materials.
Waterproofing prevents water infiltration. It involves applying membranes or coatings like bitumen, polyurethane, or PVC to block rainwater, snow, and moisture from penetrating the roof structure.
Insulation controls heat transfer. Materials like expanded polystyrene (EPS), extruded polystyrene (XPS), or polyisocyanurate (PIR) are used to improve thermal resistance (R-value), reduce energy costs, and stabilize indoor temperatures.
Which Roof Types Require Waterproofing?
These 6 roof types you should waterproof when you build them.
- Flat roof
- Gable roof
- Hip roof
- Shed roof
- Mansard roof
- Butterfly roof
What is Better Among Roof Coating and Roof Sealing Membrane?
Roof membranes are suitable for new flat roofs or full waterproofing systems, especially in high-rainfall or snow-prone zones. Coatings are best for maintenance cycles or temporary fixes when the substrate is still in fair condition.
Roof sealing membranes are generally more durable and offer superior waterproofing performance compared to coatings. These membranes, such as TPO, EPDM, PVC, and bituminous sheets, are thicker (1.2 mm to 4 mm), mechanically or chemically bonded, and resist ponding water, UV rays, and thermal movement for 15 to 30 years.
Roof coatings like acrylic, silicone, or polyurethane are liquid-applied films that provide cost-effective surface protection and reflectivity. They’re ideal for renewing aged roofs or reducing heat gain but often lack structural strength and have a shorter lifespan of 5 to 15 years.