Wood Warping: Everything You Need to Know
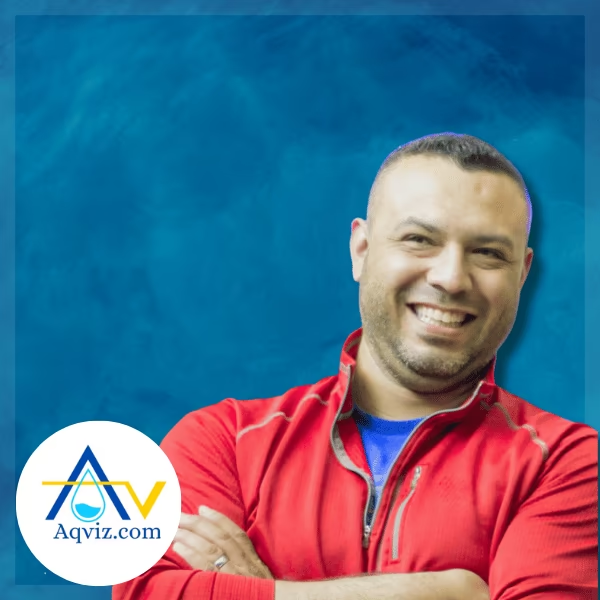
Wood warping, also known as lumber distortion, timber deformation, or board twisting, is the unnatural bending, twisting, or curving of timber due to uneven moisture content and environmental imbalances in or around the wood fibers. Wood warping occurs when the wood fibers absorb and release moisture unevenly, causing internal stress that bends or twists the board. Wood warping is mainly of 5 types, such as bowing, cupping, twisting, crooking, and gaps in joints. Wood warping can be identified by these signs.
And also these are the 6 causes for the wood warping, including uneven moisture exposure, poor drying methods, water intrusion, improper storage, fluctuating humidity, and inadequate sealing or finishing. Pine, Maple, Douglas fir, poplar, and flat-sawn lumber types are the most warped wood types. Wood is in the basement, bathroom, kitchen, crawlspace, attics, and laundry rooms. Wood is prone to warp due to higher humidity and temperature fluctuations. Wood warping can begin in as little as 24 to 72 hours if exposed to excessive moisture or intense heat, depending on the wood type and environmental conditions.
To straighten warped wood, you can use these methods, including balancing the moisture, heat, and pressure of the wood, mechanical clamping, kerf cutting, and sanding. To fix the warped wood at home, you should follow the step-by-step guide mentioned below. To prevent the wood from warping, we highly recommend you store wood properly, acclimate wood before installation, use kiln-dried lumber, apply a sealant or finish, control the indoor humidity, and install a waterproofing membrane in problematic areas in the home.
Wood warping is prolonged water damage in the home. You can use Teak wood, which has excellent warp resistance, for the home. When you see prolonged wood warping in your home, call us. We will find the problem and give you a solution.
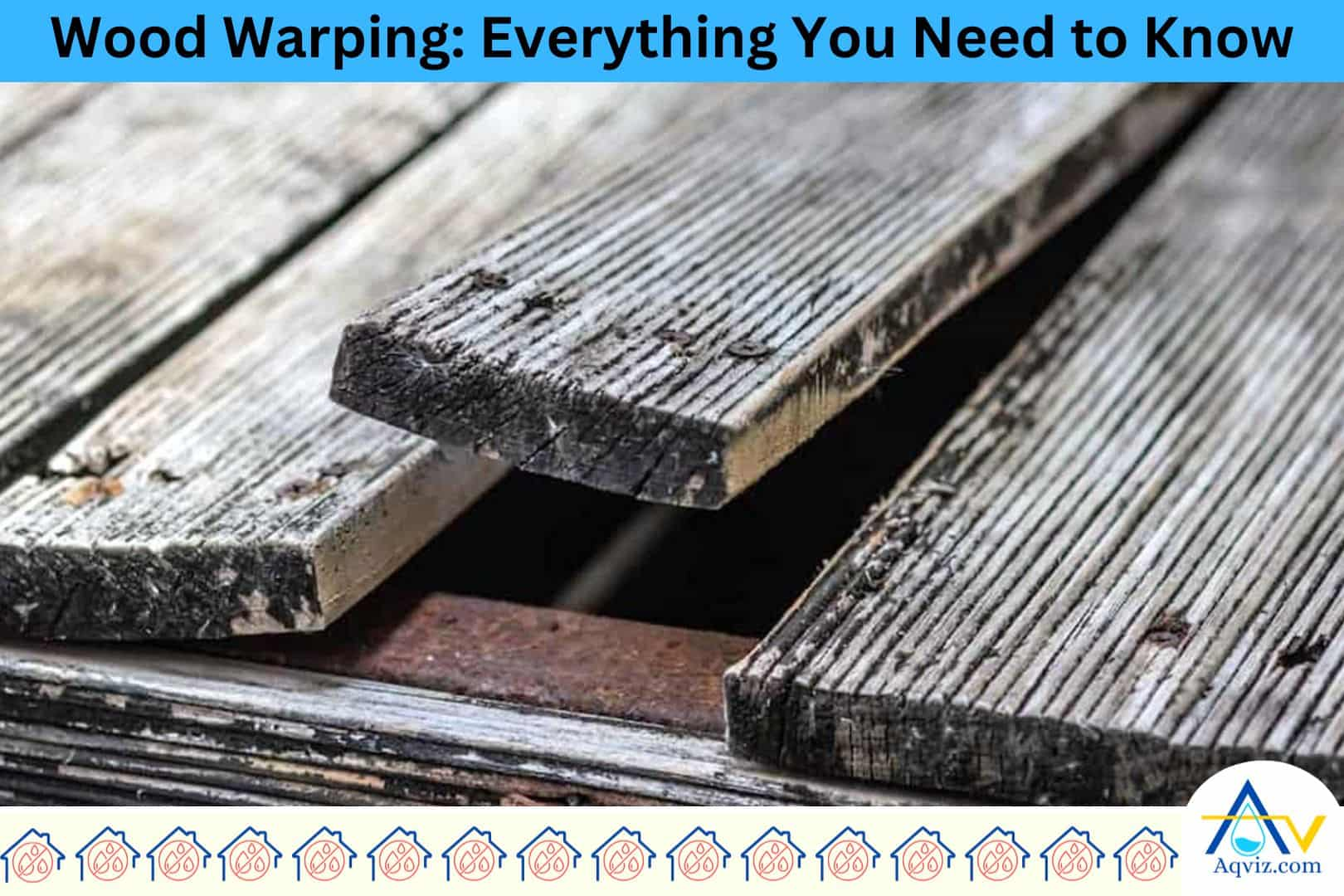
What Is the Definition of Wood Warping?
The definition of wood warping is the unnatural bending, twisting, or curving of timber due to uneven moisture content and environmental imbalances in or around the wood fibers. Wood warping occurs in water-prone areas like basements, crawl spaces, and wet foundations. Wood warping causes loss of structural integrity, misalignment of framing elements, flooring gaps, cracked drywall, and increased mold risk.
Normally, wood warping is named by other names like lumber distortion, timber deformation, or board twisting. It depends on the region or industry.
How Does Wood Warp?
Wood warping occurs when the wood fibers absorb and release moisture unevenly, causing internal stress that bends or twists the board. Wood warping happens when one side of the wood is more exposed to humidity or water leaks than the other.
Wood tends to warp when it meets these factors.
- Moisture content fluctuations : Wood swells above 20% moisture content and shrinks below 6%, triggering warping.
- Improper drying : Kiln-dried lumber should reach 6%-8% moisture before use. If not, rapid drying can twist the grain.
- Grain orientation : Flat-sawn boards warp more than quarter-sawn lumber due to uneven stress distribution.
- Environmental conditions : Areas with relative humidity above 60%, especially in basements or crawl spaces, accelerate moisture gain.
- Water intrusion : Leaks from plumbing, foundation cracks, or rising damp directly impact the wood’s ability to remain dimensionally stable.
What Are the 5 Signs of Wood Warping?
There are 5 clear signs of wood warping that every homeowner should watch for, especially in moisture-prone spaces like basements, crawl spaces, or near leaking foundations.
- Cupping : The edges of a wooden board rise while the center sinks, creating a concave surface.
- Bow : The wood curves lengthwise along the face, making the board arch or dip.
- Twist (or Wind) : Each corner of the wood turns in a different direction, creating a spiral-like deformation.
- Crook : One edge of the board bends lengthwise while the opposite edge remains straight, often seen in framing lumber.
- Gaps or misalignment : Warped floorboards, panels, or trims separate from their joints, causing visible gaps or squeaks under pressure.
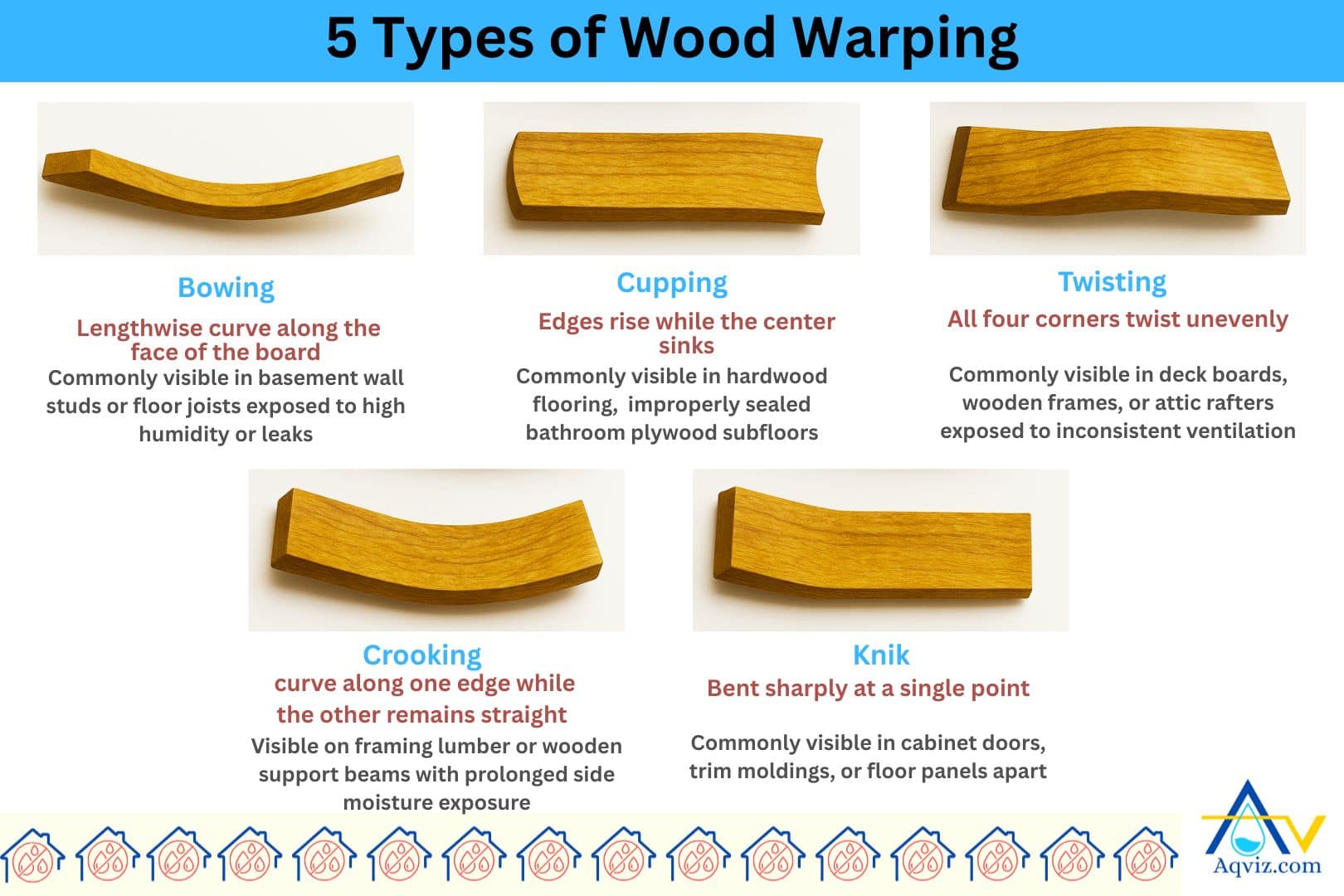
What Are the 5 Types of Wood Warping?
There are 5 primary types of wood warping we commonly observe in residential buildings, especially in damp environments.
- Bowing : A lengthwise curve along the face of the board. We usually see bowing in basement wall studs or floor joists exposed to high humidity or leaks.
- Cupping : The edges rise while the center sinks, creating a concave shape. This often appears in hardwood flooring over damp slabs or improperly sealed bathroom plywood subfloors.
- Twisting : Also called spiral distortion, where all four corners twist unevenly. This shows up in deck boards, wooden frames, or attic rafters exposed to inconsistent ventilation.
- Crooking : A curve along one edge while the other remains straight, mostly in framing lumber or wooden support beams with prolonged side moisture exposure.
- Knik : Occurs when wood is bent sharply at single point, forcing cabinet doors, trim moldings, or floor panels apart. Often seen in kitchens, bathrooms, and basements with fluctuating humidity or leaks.
What Are the 6 Causes of Wood Warping?
There are 6 main causes of wood warping due to moisture imbalance and environmental stress. These issues often appear in poorly ventilated or waterproofed areas of the home.
- Uneven moisture exposure : When one side of the wood absorbs more moisture than the other, it expands unevenly and causes distortion on the wood.
- Poor drying methods : Lumber that isn’t kiln-dried to 6%-8% moisture content warps more quickly, especially during seasonal changes.
- Water intrusion : Leaks from foundation cracks , basement seepage , or plumbing failures raise the surrounding humidity, triggering wood warping.
- Improper storage : Stacking lumber directly on concrete or outdoors without airflow can trap moisture and lead to deformation of the wood before installation.
- Fluctuating humidity : Indoor relative humidity over 60%, especially in crawl spaces or bathrooms, causes wood to absorb and release water erratically.
- Inadequate sealing or finishing : Unsealed or poorly sealed wood, particularly on decking, trim, or basement stairs, is more prone to rapid moisture shifts and surface stress on the wood.
You should know these 6 Critical Water Problems and Solutions in a House to identify and fix the wood warping in your home.
What Wood Types Warp Easily?
These 5 wood types warp easily due to their cellular structure, grain orientation, and moisture sensitivity.
- Pine : Pine is a softwood with wide grain patterns and low density. Pine absorbs moisture quickly and warps easily, especially in basements and attics with poor ventilation.
- Maple : Although maple is hard, non-porous maple tends to warp due to internal stress when exposed to uneven drying or relative humidity fluctuations above 55%.
- Douglas fir : Douglas fir is prone to crooking and bowing when stored improperly or installed in moisture-prone areas like crawl spaces.
- Poplar : Poplar is a lightweight and affordable wood type. Poplar lacks dimensional stability and can twist or cup in bathroom trims or unsealed subfloor applications.
- Flat-sawn lumber (any species) : Boards cut with the grain flat to the surface, such as flat-sawn oak or spruce, tend to cup due to uneven grain stress under humid conditions.
Where Does Wood Warp Most in the Home?
Wood warping commonly occurs in moisture-exposed and poorly ventilated areas of the home, including basements, bathrooms, kitchens, crawl spaces, attics, and laundry rooms.
- Basements : High humidity, condensation, and foundation leaks cause floor joists, studs, and subfloor wood panels to cup or twist over time.
- Bathrooms : Constant exposure to steam and water splashes in the bathroom warps vanity cabinets, door trims, and wooden flooring without proper sealing.
- Kitchens : Leaks under sinks and near dishwashers lead to buckled toe kicks, cabinet bases, and wood trims.
- Crawl spaces : Unventilated crawl spaces with ground moisture warp support beams, subfloor systems, and framing lumber, which tend to warp over time.
- Attics : Fluctuating temperatures and roof leaks cause rafters, sheathing, and storage shelves to bow or crook over time.
- Laundry rooms : Washer overflows and high humidity trigger warping in flooring and wood-based shelving.
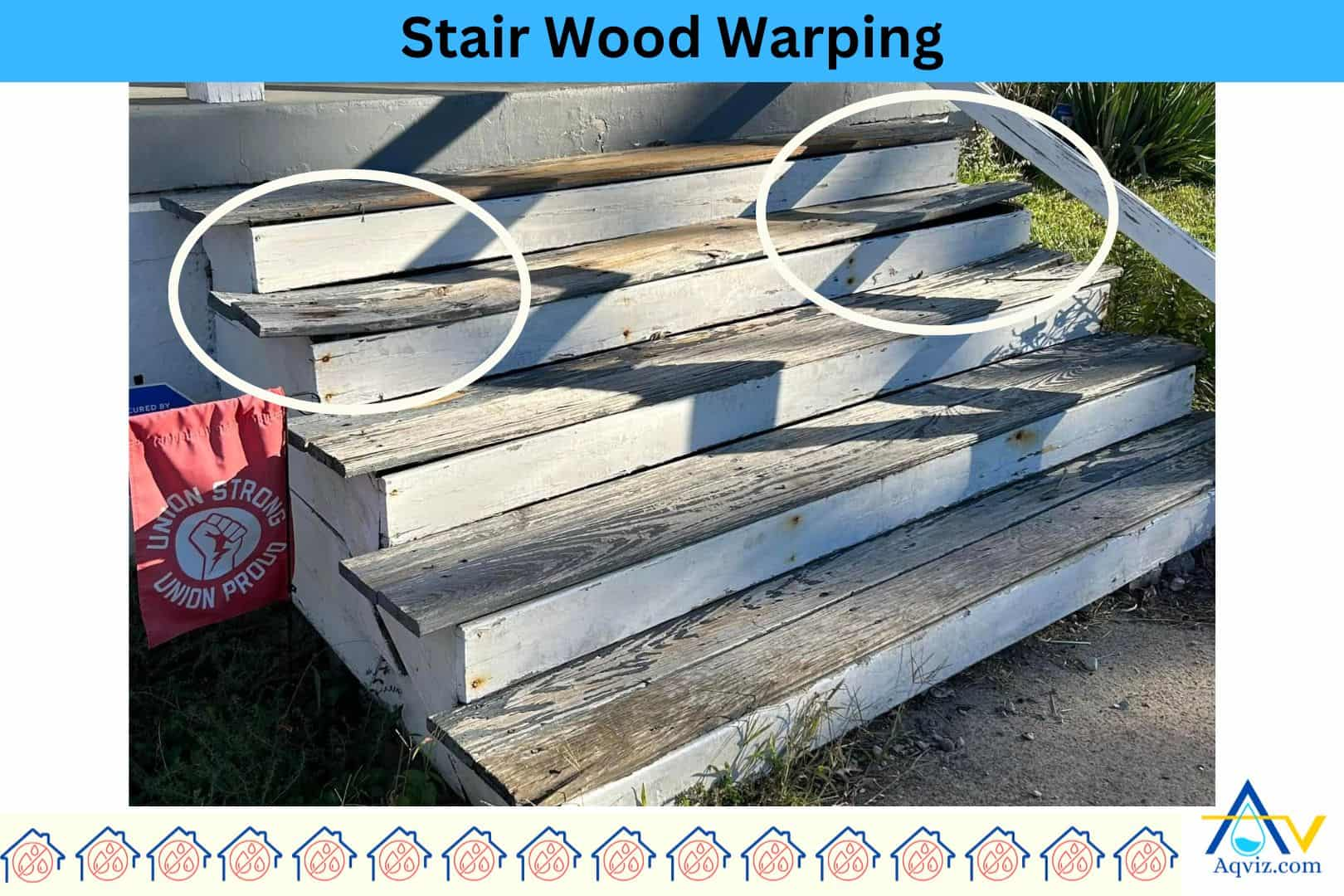
How Long Does It Take for Wood to Warp?
Wood warping can begin in as little as 24 to 72 hours if exposed to excessive moisture or intense heat, depending on the wood type and environmental conditions.
In wet conditions, such as water leaks or flooding, wood can start to cup or swell within 1 to 3 days, especially if the moisture content rises above 20%.
In hot conditions, especially under direct sunlight or attic heat above 90°F (32°C), warping can develop in 2 to 5 days, particularly if the humidity is unbalanced on either side of the wood surface.
How Do You Straighten Warped Wood?
Straightening warped wood depends on the type of warp and the extent of damage. You can use these 5 proven methods to prevent wood from warping.
- Moisture balancing : For cupped boards, you should apply moisture to the concave side and let the convex side dry in the sun. This evens out the fibers and reduces the warp.
- Heat and pressure : You should use a heat gun or steam, then clamp the board flat for 24-48 hours. This method works well for twisting and bowing in decking or framing.
- Mechanical clamping : You should place warped wood between flat surfaces with clamps and leave it in a dry, controlled environment to slowly realign over several days.
- Kerf cutting : For severe crook or bow, you should cut relief grooves along the back to release tension. This method is common with trim boards and subfloor panels.
- Planing or sanding : If warping is minimal, you should remove the high spots with a hand planer or belt sander. This is useful in floors or countertops.
How to Fix Warped Wood?
Fixing warped wood involves reversing the distortion and restoring structural shape. You should follow this step-by-step guide from our experts based on years of experience.
- Identify the type of warp: Check if the wood shows cupping, bowing, twisting, or crooking. Each type requires a different technique.
- Measure the moisture content: Use a moisture meter to check if it’s above 15%. If yes, place the wood in a dry, ventilated space to stabilize before starting repairs.
- Apply moisture or heat: For cupped or bowed boards, dampen the concave side with a wet cloth. Then, expose the convex side to sunlight or use a heat gun carefully to balance fiber stress.
- Clamp the wood flat : Place the board between two flat, straight surfaces. Apply uniform clamping pressure and leave it for 24-72 hours. For twisted boards, use crosswise clamping.
- Add kerf cuts (if necessary): For stubborn crooks or bows, cut shallow relief grooves along the back side using a circular saw. This relieves tension and helps straighten the board.
- Plane or sand to level: After reshaping, use a hand planer or sander to smooth any uneven surfaces and restore proper thickness.
- Seal the wood: Apply a waterproof wood sealer, especially if the board is in a humid area like a basement, kitchen, or bathroom, to prevent future warping.
How to Prevent Wood Warping?
Preventing wood warping requires controlling moisture exposure and ensuring proper handling from storage to installation. You should follow this 6-step guide to avoid future wood warping, in high-risk damp zones like basements, bathrooms, and crawl spaces.
- Store wood properly: You should keep wood stacked flat on a raised surface with spacers between boards for airflow. Avoid direct contact with concrete floors or damp areas.
- Acclimate wood before installation: You should let the wood sit in the room where it will be installed for at least 72 hours. This allows it to adjust to the temperature and humidity.
- Use kiln-dried lumber: You should choose kiln-dried wood with a moisture content between 6%-8%, especially for indoor use. Avoid green or wet lumber for structural framing.
- Apply sealant or finish: You should coat all sides, including ends and hidden surfaces, with a quality wood sealant or waterproof finish like polyurethane or epoxy resin.
- Control indoor humidity: You should use dehumidifiers and maintain indoor relative humidity between 40%-60%, particularly in basements, bathrooms, and laundry rooms.
- Install waterproofing systems: You should apply vapor barriers and waterproof membranes and ensure proper drainage in areas exposed to moisture. At Aqviz, we often install sump pumps , moisture barriers , and foundation sealants to protect the wood structures
Wood rotting is another wood damage in the home due to excessive water. Wood Rotting: Everything You Need to Know guide includes all the important causes, signs, prevention methods and many more related to wood rotting.
Can Waterproofing Stop Wood Warping?
Yes, waterproofing can effectively stop wood warping by eliminating the root cause: water and moisture. A waterproofing system helps to seal all the cracks and damages on the surface, which are prone to leaking and allowing water through the substrate. This helps to control the moisture and water content in the area that affects the wood from warping.
Can Wood Warp From Heat?
Yes, wood can warp from heat, especially when high temperatures cause uneven drying across the wood’s surface. Timber deformation and board twisting occur in areas like attics, sunrooms, and unshaded decks, where the temperature regularly exceeds 90°F (32°C).
When heat dries one side of the wood faster than the other, it creates internal stress, pulling the fibers out of alignment. If the wood moisture content drops below 6%, the board may cup, bow, or twist, especially in species like pine, fir, or flat-sawn oak.
Does Teak Wood Warp?
Teak wood rarely warps, thanks to its high natural oil content, tight grain, and excellent dimensional stability. Therefore, teak wood is highly recommended for outdoor decks, bathroom vanities, and high-humidity zones, because it resists both water absorption and thermal expansion better than most hardwoods.
Even under high humidity or direct sun exposure, teak maintains its shape if it’s properly sealed and ventilated. However, improper installation or prolonged saturation without airflow can still cause minor cupping or surface movement. For best performance, we advise using marine-grade sealers and ensuring adequate air circulation around all teak surfaces.
Does Cedar Wood Warp?
Yes, cedar wood can warp, but it’s less prone than many softwoods due to its natural oils, low density, and resistance to moisture decay. Hence, you can use western red cedar for siding, trim, and outdoor fencing, but you will see board twisting and cupping when cedar isn’t properly dried or sealed over time with exposure to moisture.
Does Faux Wood Warp?
Yes, faux wood can warp, especially low-grade medium-density fiberboard (MDF) or plastic-composite trims used in high-humidity spaces. Faux wood baseboards, crown moldings, or interior doors are distorted due to steam exposure, plumbing leaks, or poor ventilation in bathrooms and laundry rooms.
Unlike solid wood, faux wood may delaminate or bubble when exposed to moisture levels above 60% RH. The adhesive resins inside the product break down, causing structural failure. To reduce risk, we recommend using moisture-resistant MDF, applying primer-grade sealers, and installing faux wood only in dry, well-ventilated areas.
Is Wood Warping a Sign of Water Damage?
Yes, wood warping is often a clear sign of water damage , especially in high-risk areas like basements, crawl spaces, and bathrooms. When wood absorbs excess moisture, it expands unevenly. Over time, this triggers visible warping on the wood. That is why you can see board twisting, cupping, and lumber distortion back to underlying issues such as leaking pipes, foundation seepage, or poor drainage systems.